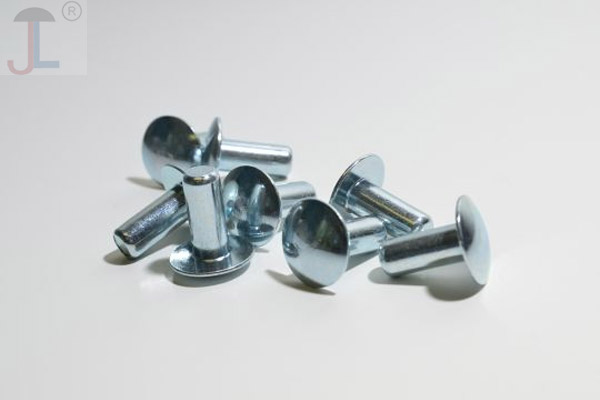
The strength of aluminum rivets varies significantly based on several factors, including:
Aluminum Alloy: Different aluminum alloys have different inherent strengths. For example, 1100-grade aluminum rivets are considered "soft" with a tensile strength of around 16,000 PSI, while 2117 aluminum rivets heat-treated to the T4 condition ("AD" rivets) have a shear strength of about 26,000 PSI and a tensile strength of approximately 38,000 PSI.
Rivet Type and Size: The diameter and style of the rivet head (e.g., dome, countersunk, large flange) influence its strength. Larger diameter rivets generally offer higher strength.
Construction: Some rivets have an aluminum body with a steel mandrel, which can affect the overall strength characteristics. Steel and stainless steel rivets generally have higher tensile and shear strength than all-aluminum rivets.
Shear vs. Tensile Strength: Rivets are typically designed to withstand shear loads (forces acting parallel to the joined materials). Their tensile strength (resistance to pulling forces) is usually lower.
Approximate Strength Ranges (Keep in Mind These Are General):
For aluminum rivets with a steel body, some typical minimum strength values are:
Shear Strength:
1/8" diameter: 170 lbs
5/32" diameter: 260 lbs
3/16" diameter: 380 lbs
Tensile Strength:
1/8" diameter: 220 lbs
5/32" diameter: 350 lbs
3/16" diameter: 500 lbs
For all-aluminum rivets, here are some examples:
A 3/16" diameter all-aluminum bulb-type rivet can have a shear strength around 202 lbs and a tensile strength of about 247 lbs.
A 1/4" diameter all-aluminum pop rivet might have a shear strength of approximately 460 lbs and a tensile strength of about 560 lbs.
For a 3/16" diameter standard blind rivet with an aluminum body and mandrel, the shear strength can be around 260 lbs and the tensile strength around 320 lbs.
Important Considerations:
Galvanic Corrosion: When joining aluminum parts, it's generally recommended to use aluminum rivets to avoid galvanic corrosion that can occur when dissimilar metals (like stainless steel) are in contact.
Application: The required strength of the rivets depends heavily on the specific application and the loads it will need to withstand.
The strength of aluminum rivets varies significantly based on several factors, including:
Aluminum Alloy: Different aluminum alloys have different inherent strengths. For example, 1100-grade aluminum rivets are considered "soft" with a tensile strength of around 16,000 PSI, while 2117 aluminum rivets heat-treated to the T4 condition ("AD" rivets) have a shear strength of about 26,000 PSI and a tensile strength of approximately 38,000 PSI.
Rivet Type and Size: The diameter and style of the rivet head (e.g., dome, countersunk, large flange) influence its strength. Larger diameter rivets generally offer higher strength.
Construction: Some rivets have an aluminum body with a steel mandrel, which can affect the overall strength characteristics. Steel and stainless steel rivets generally have higher tensile and shear strength than all-aluminum rivets.
Shear vs. Tensile Strength: Rivets are typically designed to withstand shear loads (forces acting parallel to the joined materials). Their tensile strength (resistance to pulling forces) is usually lower.
Approximate Strength Ranges (Keep in Mind These Are General):
For aluminum rivets with a steel body, some typical minimum strength values are:
Shear Strength:
1/8" diameter: 170 lbs
5/32" diameter: 260 lbs
3/16" diameter: 380 lbs
Tensile Strength:
1/8" diameter: 220 lbs
5/32" diameter: 350 lbs
3/16" diameter: 500 lbs
For all-aluminum rivets, here are some examples:
A 3/16" diameter all-aluminum bulb-type rivet can have a shear strength around 202 lbs and a tensile strength of about 247 lbs.
A 1/4" diameter all-aluminum pop rivet might have a shear strength of approximately 460 lbs and a tensile strength of about 560 lbs.
For a 3/16" diameter standard blind rivet with an aluminum body and mandrel, the shear strength can be around 260 lbs and the tensile strength around 320 lbs.
Important Considerations:
Galvanic Corrosion: When joining aluminum parts, it's generally recommended to use aluminum rivets to avoid galvanic corrosion that can occur when dissimilar metals (like stainless steel) are in contact.
Application: The required strength of the rivets depends heavily on the specific application and the loads it will need to withstand.