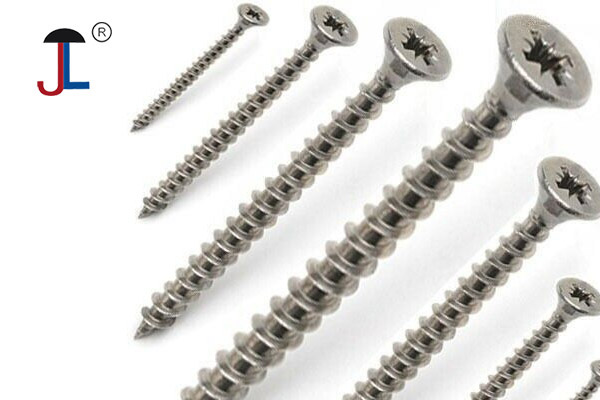
Chemical Composition:
A2 (304) typically contains around 18% chromium and 8% nickel. A4 (316) also contains 18% chromium and approximately 10-12% nickel, but the crucial difference is the addition of 2% molybdenum, which significantly enhances corrosion resistance.
Corrosion Resistance:
A4's molybdenum content gives it superior corrosion resistance, particularly against chloride-rich environments like saltwater and certain industrial chemicals. A2 has good corrosion resistance for general use but may not be suitable for highly corrosive environments.
Applications:
A2 is commonly used in various applications, including food processing equipment, kitchen equipment, and automotive parts where moderate corrosion resistance is sufficient. A4, due to its exceptional corrosion resistance, is often preferred in marine environments, chemical processing, and other demanding applications.
Cost:
A4 typically costs more than A2 due to the added molybdenum and its enhanced properties.
Workability:
While both grades are generally easy to work with, A4 fasteners are sometimes slightly easier to fabricate, clean, finish, and weld compared to A2 due to its chemical composition.
In essence, A4 is a more robust and corrosion-resistant grade compared to A2, making it the preferred choice for applications requiring higher protection against corrosion and demanding environments.